生産管理
製品や部品を効率的にムダなく作っていくためのいろいろな手法を活かしていくのが生産管理です。中小企業の効率的な生産システムの再構築や問題点の改善。生産性向上対策、組立工程の改善や問題点の解決。工程能力問題の改善などが主たる活動です。
|
品質管理
ものづくりの作業や工程のなかで、製品の品質は、常に変化していることを先ず知っておくことです。その製品の品質を確保していく手法が品質管理です。製造品質の向上、工程検査の改善、工程能力の改善、不良低減、クレーム対策や現場での問題点の調査と改善などに取り組みます。
|
製造コスト低減
製造コストの低減は、ものづくり企業の最も要求される課題です。設計、製造、購買部門など各部門のコスト低減活動が求められます。コスト低減の手法として、VA、VEの実践、調達品や購買品のコストテーブル、ベンチマークの活用などがあります。さらに、原価計算や固有技術の基礎的な知識教育も課題です。
|
現場管理
ものづくりの力の源泉は、現場の力にあると考えています。現場を強くすることが先ず必要です。第一線監督者の現場管理能力向上、監督者教育、現場改善手法、部下のOJT訓練計画と実施、現場におけるQC教育と実践活動の支援などを行ないます。
|
外注メーカー支援
外注メーカーは、発注企業の工場の一つです。したがって、社内工場と同じ視点で取り組む必要があります。社内工場と外注メーカーは密接につながっていますから、外注メーカー問題点の改善解決や外注企業の生産性向上、コスト削減、納期遅れなど問題点の解決に取り組んでいきます。
|
海外工場計画と工場建設
海外工場建設のための現地調査から海外工場の事業計画、工場建設までの技術支援を行ないます。
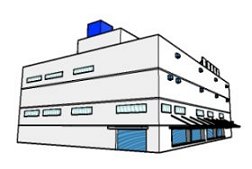 |
海外進出支援
海外生産を行なうには、事前にいろいろな調査や準備事項があります。海外生産を成功させるためには、海外生産に経験と知識を有する専門化の協力は欠かせません。海外生産に関する支援例えば、技術協力契約、ロイヤルティなどに関する事項、海外事業計画などは重要な検討事項です。
海外生産で問題となる自社の技術の流失をどうのように防ぐかは、重要な問題点の一つです。
|
海外自動車組立技術支援
海外自動車メーカーの品質向上支援や新車種の生産準備(設備計画や組立治具計画など)に関する技術支援を行なっています。
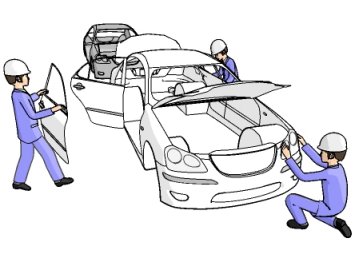 |
自動車組立技術支援
自動車組立技術の中で、専門は車体組立(Body Assembly)技術です。組立治具、検査具計画や設計支援。組立品質向上、設備計画、工程計画や外注メーカー指導などを行ないます。車体組立はプレスパネルの溶接が中心ですが、同時に溶接ロボットによる溶接、自動化ラインとなっています。さらに、新車開発段階でのSE(後述)や車体品質改善にも取り組んでいます。
|
製品組立技術
製品の組立について、生産技術的な側面から考えたいと思います。製品はその機能や性能を発揮させるために、多くの必要な部品から構成されています。この部品をどのように設計するか、又はどのように組立てていくか、良い製品を作るためには、いろいろな技術的、コスト的な課題があります。
|